MDI PTMEG Prepolymers
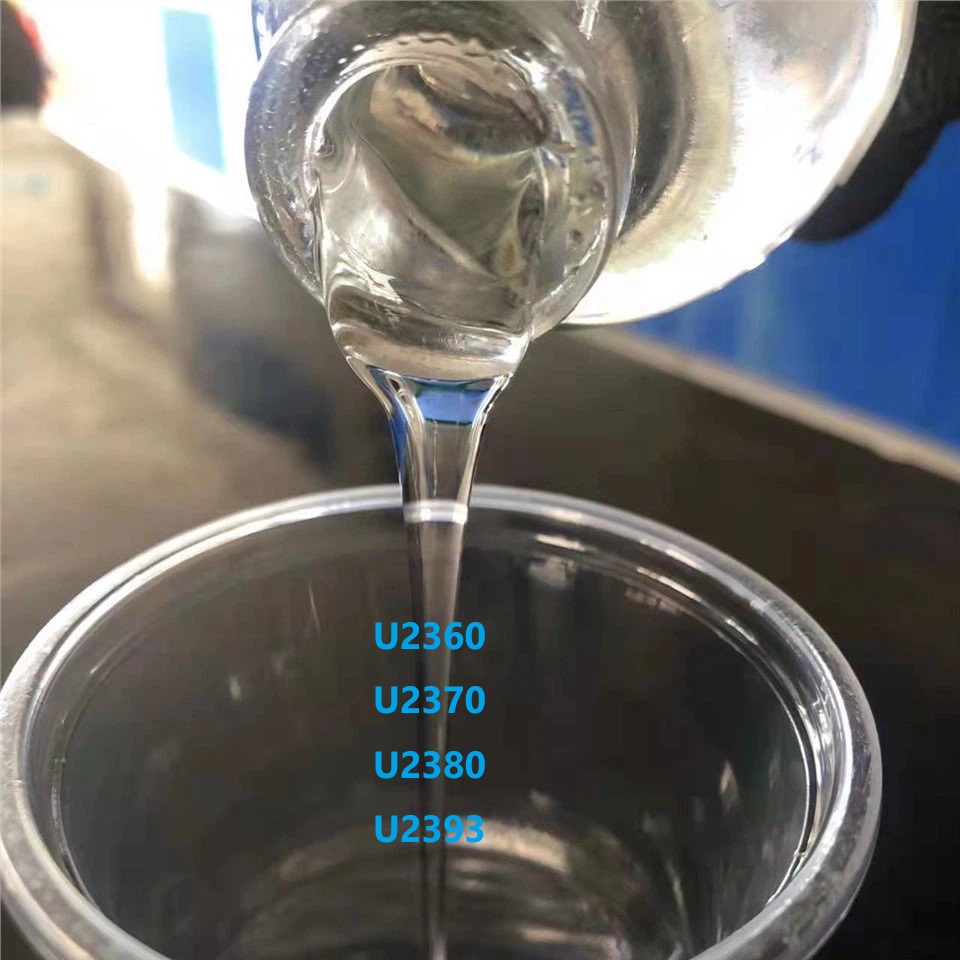
Index | U2360 | U2370 | U2380 | U2393 |
NCO Content (%) | 6.0±0.2 | 7.0±0.2 | 8.0±0.2 | 9.3±0.2 |
Operating Conditions | ||||
Ratio (Poly: BDO) | 100:6.30 | 100:7.35 | 100:8.40 | 100:9.76 |
Prepolymer Temp (°C) | 85 | 80 | 75 | 75 |
Curing Agent Temp (°C) | 40 | 40 | 40 | 40 |
Mold Temp (°C) | 110-120 | 110-120 | 110-120 | 110-120 |
Pot Life (min) | 6-7 | 4-5 | 3-4 | 2-3 |
Demold Time (min) | 30-40 | 30 | 30 | 30 |
After Cure (h/100°C) | 16 | 16 | 16 | 16 |
Physical Performance | ||||
Shore Hardness (A) | 80±2 | 85±2 | 90±2 | 95±2 |
100% Modulus (MPa) | 4 | 6 | 8 | 9 |
300% Modulus (MPa) | 9 | 12 | 16 | 20 |
Ultimate Elongation (%) | 590 | 568 | 520 | 480 |
Tensile Strength (MPa) | 25 | 40 | 45 | 47 |
Tear Strength (without Nick) (KN/m) | 78 | 92 | 106 | 112 |
Resilience (%) | 58 | 54 | 52 | 45 |
DIN Abrasion (mm³) | 38 | 35 | 35 | 38 |
Density (25℃) (g/cm³) | 1.11 | 1.12 | 1.12 | 1.13 |
MDI PTMEG (Polytetramethylene Ether Glycol) Prepolymers are highly regarded in various industries for their exceptional performance characteristics. These prepolymers, when combined with Methylene Diphenyl Diisocyanate (MDI), form polyurethane systems with a unique balance of mechanical strength, flexibility, and resistance to various environmental factors. Below are the key advantages and applications of MDI PTMEG prepolymers:
Advantages of MDI PTMEG Prepolymers
1. Outstanding Mechanical Properties
· High Tensile Strength and Toughness: MDI PTMEG-based polyurethanes provide exceptional tensile strength, ensuring durability in demanding applications. The material can withstand heavy loads, making it ideal for industrial uses.
· Excellent Tear and Abrasion Resistance: These prepolymers are known for their superior resistance to tearing and abrasion, essential for parts subjected to mechanical wear and friction, such as conveyor belts and seals.
2. Exceptional Hydrolysis Resistance
· Water and Moisture Stability: PTMEG-based polyurethanes exhibit excellent resistance to hydrolysis, which allows them to maintain their integrity and performance in moist or underwater conditions. This makes them suitable for use in humid environments or for applications exposed to water.
3. High Flexibility and Elasticity
· Long-Lasting Elasticity: MDI PTMEG prepolymers provide polyurethanes with excellent flexibility and elasticity, even at low temperatures. This characteristic makes the material ideal for applications requiring repeated deformation without losing its form, such as elastomers and seals.
4. Low Temperature Performance
· Retains Mechanical Properties at Low Temperatures: MDI PTMEG polyurethanes remain flexible and maintain their mechanical properties at low temperatures, making them suitable for cold-climate or freezer applications without becoming brittle.
5. Enhanced Chemical Resistance
· Resistance to Oils and Chemicals: PTMEG-based systems are highly resistant to oils, fuels, and various chemicals, making them suitable for applications exposed to aggressive substances, such as automotive parts, fuel lines, and seals.
6. Biocompatibility
· Potential for Medical Applications: PTMEG-based polyurethanes are known for their biocompatibility, allowing them to be used in medical and healthcare applications, such as medical devices, wound dressings, and implants.
7. Good Dynamic Properties
· Fatigue Resistance: PTMEG polyurethanes exhibit excellent dynamic properties, meaning they can withstand cyclic stress and repeated flexing without deteriorating, which is critical for products like gaskets, vibration dampeners, and tires.
8. Ease of Processing
· Customizable: The prepolymers allow for easy processing and customization of polyurethane formulations. By adjusting component ratios, manufacturers can tailor the properties of the end product, such as hardness, flexibility, and curing speed.
Applications of MDI PTMEG Prepolymers
1. Elastomers
· High-Performance Elastomers: MDI PTMEG prepolymers are commonly used in manufacturing high-performance polyurethane elastomers that require a combination of durability, flexibility, and resistance to harsh environments. These elastomers are used in automotive parts, industrial rollers, and conveyor belts.
2. Seals and Gaskets
· Long-Lasting Sealing Materials: Due to their resistance to oils, chemicals, and water, MDI PTMEG polyurethanes are used in seals and gaskets for industrial machinery, automotive engines, and other systems requiring robust sealing under dynamic conditions.
3. Wheels and Tires
· Durable and Abrasion-Resistant: These prepolymers are ideal for manufacturing wheels and tires used in heavy industrial equipment, skateboards, and medical devices, where excellent abrasion resistance and load-bearing capacity are essential.
4. Hoses and Tubing
· Chemical-Resistant Tubing: Polyurethanes made from MDI PTMEG prepolymers are often used in hoses and tubing for chemical transport, fuel lines, and hydraulic systems due to their excellent flexibility and resistance to degradation from oils and fuels.
5. Coatings
· Protective Coatings: MDI PTMEG-based polyurethane coatings are applied to surfaces that require protection from abrasion, chemicals, and weathering. These coatings are used in industrial machinery, pipelines, and marine applications.
6. Adhesives
· High-Performance Adhesives: The excellent bonding strength and flexibility of MDI PTMEG prepolymers make them a reliable choice for high-performance adhesives, especially in the automotive, aerospace, and construction industries.
7. Vibration Dampeners
· Noise and Vibration Control: MDI PTMEG polyurethanes are used in vibration dampening applications due to their elasticity and energy absorption properties. This makes them suitable for products like shock absorbers, mounts, and vibration pads.
8. Medical Devices
· Biocompatible Polyurethanes: With their good mechanical properties and biocompatibility, MDI PTMEG prepolymers are also used in medical devices, including implants, catheter tubing, and medical-grade elastomers.
9. Industrial Rollers
· Durable Roller Applications: MDI PTMEG polyurethanes are used in the production of industrial rollers due to their ability to resist abrasion, maintain elasticity, and perform well under high loads.
Summary
MDI PTMEG prepolymers offer a unique combination of strength, flexibility, chemical resistance, and hydrolytic stability. These properties make them a preferred material in industries requiring durable elastomers, seals, coatings, and adhesives, especially where exposure to moisture, chemicals, and varying temperatures is common.