MDI Polyester Prepolymers
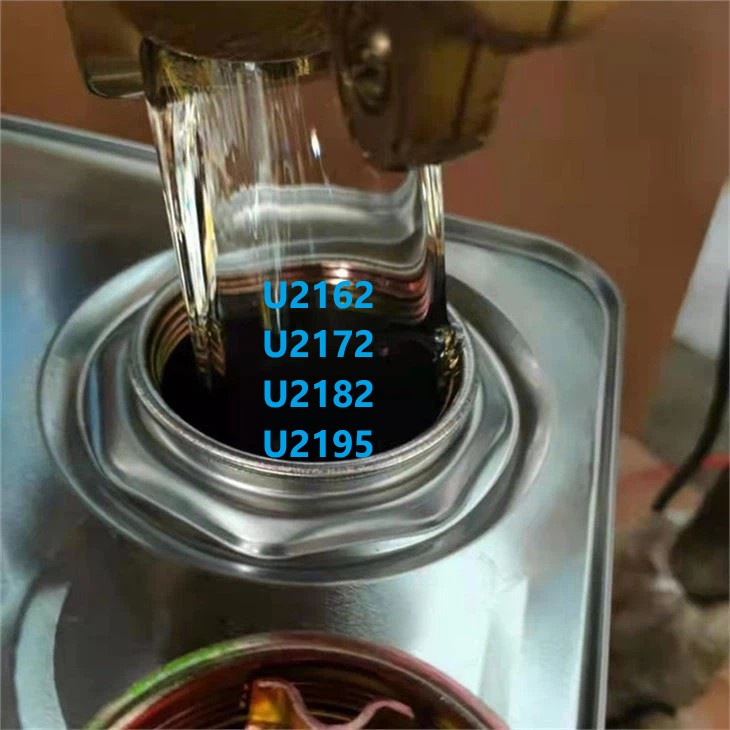
Index | U2162 | U2172 | U2182 | U2195 |
NCO Content (%) | 6.2±0.2 | 7.2±0.2 | 8.2±0.2 | 9.5±0.2 |
Operating Conditions | ||||
Ratio (Poly: BDO) | 100:6.51 | 100:7.56 | 100:8.61 | 100:9.97 |
Prepolymer Temp (°C) | 85 | 80 | 75 | 75 |
Curing Agent Temp (°C) | 40 | 40 | 40 | 40 |
Mold Temp (°C) | 110-120 | 110-120 | 110-120 | 110-120 |
Pot Life (min) | 5-6 | 4-5 | 3-4 | 2-4 |
Demold Time (min) | 30-40 | 30 | 30 | 30 |
After Cure (h/100°C) | 16 | 16 | 16 | 16 |
Physical Performance | ||||
Shore Hardness (A) | 80±2 | 85±2 | 90±2 | 95±2 |
100% Modulus (MPa) | 5 | 8 | 9 | 9 |
300% Modulus (MPa) | 13 | 17 | 18 | 19 |
Ultimate Elongation (%) | 638 | 590 | 560 | 520 |
Tensile Strength (MPa) | 42 | 45 | 47 | 49 |
Tear Strength (without Nick) (KN/m) | 95 | 106 | 112 | 118 |
Resilience (%) | 45 | 42 | 40 | 36 |
DIN Abrasion (mm³) | 38 | 40 | 42 | 50 |
Density (25℃) (g/cm³) | 1.23 | 1.24 | 1.24 | 1.26 |
MDI Polyester Prepolymers combine Methylene Diphenyl Diisocyanate (MDI) with polyester polyols to create high-performance polyurethane materials with a range of advantageous properties. These prepolymers are widely used in various industries due to their unique balance of strength, chemical resistance, and durability. Below are the key advantages and applications of MDI Polyester Prepolymers:
Advantages of MDI Polyester Prepolymers
1. High Tensile and Tear Strength
· Mechanical Strength: MDI polyester-based polyurethanes are known for their excellent tensile strength and tear resistance, making them ideal for applications where mechanical durability and robustness are essential.
2. Outstanding Abrasion Resistance
· Durability in High-Friction Applications: MDI polyester prepolymers provide superior abrasion resistance, making them suitable for applications exposed to wear and tear, such as industrial machinery, belts, and gaskets.
3. Excellent Chemical Resistance
· Resistance to Oils and Solvents: MDI polyester prepolymers exhibit strong resistance to oils, fuels, and many chemicals, outperforming polyether-based polyurethanes in certain chemical environments. This property is crucial for products exposed to aggressive chemicals or oils, such as in automotive and industrial applications.
4. Good Heat Resistance
· Stability at Higher Temperatures: These prepolymers offer good thermal stability and can maintain their mechanical properties at elevated temperatures, making them useful in high-temperature environments compared to polyether-based polyurethanes.
5. High Load-Bearing Capacity
· Elasticity Under Load: MDI polyester prepolymers provide a high load-bearing capacity and maintain elasticity under stress, which is important for applications that involve heavy loads, such as wheels, tires, and conveyor belts.
6. Improved Weather Resistance
· UV and Environmental Resistance: These prepolymers exhibit good resistance to environmental factors like UV radiation and weathering, contributing to the longevity of outdoor products and equipment.
7. Controlled Hardness
· Versatile Formulation: MDI polyester prepolymers allow manufacturers to control the hardness of the resulting polyurethane by adjusting the prepolymer formulation. This makes them highly versatile for different applications, from flexible elastomers to rigid coatings.
8. Long-Term Stability
· Slow Degradation in Harsh Conditions: Polyester-based polyurethanes made with MDI generally degrade more slowly than polyether-based ones in harsh chemical environments, providing longer-term durability and reliability in demanding industrial uses.
Applications of MDI Polyester Prepolymers
1. Elastomers
· High-Performance Elastomers: MDI polyester prepolymers are used in the production of high-performance polyurethane elastomers. These elastomers are employed in demanding industrial applications requiring excellent mechanical strength, flexibility, and abrasion resistance, such as wheels, bumpers, and mechanical parts.
2. Seals and Gaskets
· Chemical-Resistant Seals: These prepolymers are ideal for manufacturing seals and gaskets that need to withstand harsh chemical environments, high temperatures, and dynamic loading, making them suitable for use in the automotive, oil, and gas industries.
3. Industrial Rollers and Conveyor Belts
· Abrasion-Resistant Components: MDI polyester-based polyurethanes are used to make rollers and conveyor belts that are subject to constant abrasion and wear, offering long-lasting durability and maintaining their structural integrity over time.
4. Wheels and Tires
· Heavy-Duty Wheels: Due to their high load-bearing capacity, wear resistance, and ability to absorb impact, MDI polyester prepolymers are used in manufacturing wheels and tires for heavy equipment, industrial machinery, and even recreational products like skateboards or roller skates.
5. Adhesives
· High-Performance Adhesives: MDI polyester prepolymer-based adhesives are used in applications requiring strong bonding under chemical exposure, elevated temperatures, or high mechanical stresses, such as in automotive and construction applications.
6. Coatings
· Protective Coatings: MDI polyester prepolymers are used to formulate coatings that require excellent resistance to abrasion, chemicals, and weathering. These coatings are applied to surfaces such as pipes, equipment, and industrial floors to protect against wear, corrosion, and environmental damage.
7. Molded Parts
· Precision Molded Components: Due to their ability to be easily processed and shaped, MDI polyester prepolymers are used to manufacture precision-molded parts for various industrial applications, including automotive components, bushings, and insulators.
8. Foams
· High-Density Foams: MDI polyester prepolymers can be used to create high-density polyurethane foams that provide cushioning and insulation in demanding applications. These foams are used in seating, padding, and packaging for heavy-duty and industrial applications.
Summary
MDI Polyester Prepolymers offer a wide range of advantages, including high mechanical strength, excellent chemical and abrasion resistance, good thermal stability, and long-term durability. These characteristics make them an excellent choice for industries that require robust, high-performance polyurethane materials, particularly in the fields of elastomers, seals, industrial rollers, wheels, coatings, and adhesives. Their ability to perform under challenging environmental and mechanical conditions makes them a popular choice for a variety of demanding applications.