NDI-based Prepolymers
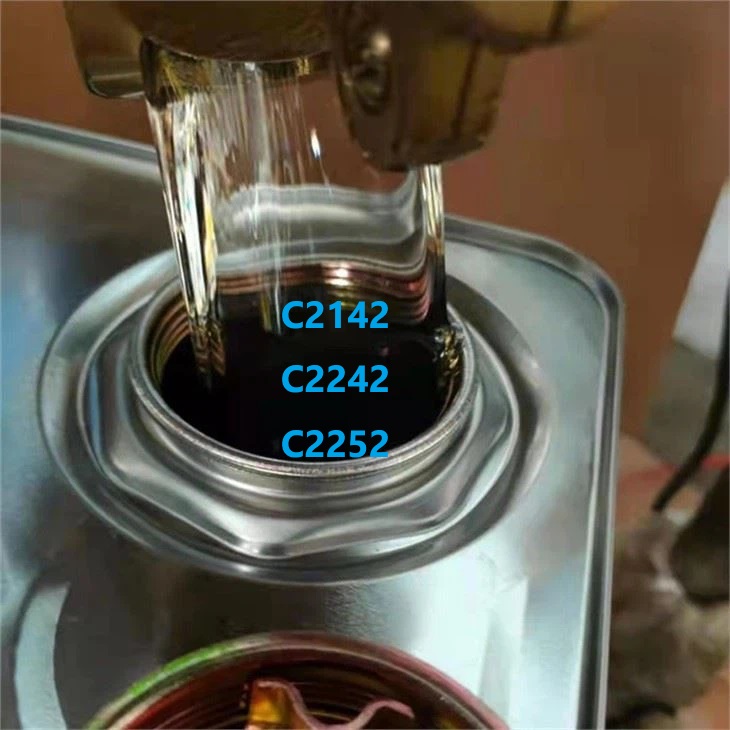
Index | C2142 | C2242 | C2252 |
NCO Content (%) | 4.2±0.2 | 4.2±0.2 | 5.2±0.2 |
Operating Conditions | |||
Ratio (Poly: BDO) | 100:4.41 | 100:4.41 | 100:5.25 |
Prepolymer Temp (°C) | 90 | 90 | 85 |
Curing Agent Temp (°C) | 30 | 30 | 30 |
Mold Temp (°C) | 110-120 | 110-120 | 110-120 |
Pot Life (min) | 3-5 | 3-5 | 2-4 |
Demold Time (min) | 30-40 | 30-40 | 30-40 |
After Cure (h/100°C) | 16 | 16 | 16 |
Physical Performance | |||
Shore Hardness (A) | 95±2 | 95±2 | 98±1 |
100% Modulus (MPa) | 11 | 8 | 14 |
300% Modulus (MPa) | 18 | 15 | 22 |
Ultimate Elongation (%) | 505 | 527 | 482 |
Tensile Strength (MPa) | 47 | 42 | 49 |
Tear Strength (without Nick) (KN/m) | 146 | 142 | 156 |
Resilience (%) | 67 | 53 | 54 |
DIN Abrasion (mm³) | 39 | 42 | 42 |
Density (25℃) (g/cm³) | 1.24 | 1.18 | 1.19 |
NDI Prepolymers (Naphthalene Diisocyanate-based prepolymers) are highly regarded for their exceptional mechanical properties, thermal stability, and chemical resistance. These prepolymers are commonly used in applications requiring high performance, durability, and toughness, particularly in the production of high-performance polyurethanes. Here are the key advantages and applications of NDI prepolymers:
Advantages of NDI Prepolymers
1. Superior Mechanical Properties
· High Tensile Strength and Toughness: NDI-based polyurethanes exhibit superior tensile strength, toughness, and durability. These properties make them suitable for applications that involve heavy loads and mechanical stress.
· Excellent Tear and Abrasion Resistance: NDI prepolymers provide polyurethanes with outstanding tear and abrasion resistance, making them ideal for high-friction environments, such as in wheels, conveyor belts, and seals.
2. Outstanding Heat Resistance
· Thermal Stability: One of the key advantages of NDI prepolymers is their excellent heat resistance. They maintain their mechanical properties and stability at high temperatures, outperforming other isocyanate-based systems like MDI or TDI. This makes them suitable for use in high-temperature environments where thermal degradation is a concern.
3. Enhanced Chemical Resistance
· Resistance to Harsh Chemicals: NDI polyurethanes offer enhanced resistance to chemicals, oils, and fuels. This property is crucial for applications in environments where chemical exposure is frequent, such as industrial equipment, automotive components, and aerospace applications.
4. Good Low-Temperature Performance
· Retains Flexibility in Cold Environments: In addition to their thermal stability at high temperatures, NDI prepolymers also maintain flexibility and toughness at low temperatures, making them suitable for applications in cold climates or in environments with large temperature variations.
5. Long-Term Durability
· Fatigue and Creep Resistance: NDI-based polyurethanes offer excellent fatigue resistance, meaning they can withstand repeated stress cycles without significant degradation. They also show superior creep resistance, making them ideal for applications that involve constant load-bearing over time.
6. Hydrolysis Resistance
· Stability in Moist Environments: NDI prepolymers exhibit good hydrolytic stability, allowing them to perform well in humid or moist environments without breaking down or losing mechanical properties.
7. Low Compression Set
· Elastic Recovery: NDI-based polyurethanes tend to have a low compression set, meaning they retain their shape and elasticity even after prolonged compression. This characteristic is important for applications requiring long-term resilience and load-bearing capacity.
8. Longer Service Life
· High-Endurance Applications: Due to their combination of mechanical strength, thermal stability, and chemical resistance, NDI polyurethanes often have a longer service life compared to other polyurethane systems. This results in reduced maintenance and replacement costs in industrial applications.
Applications of NDI Prepolymers
1. High-Performance Elastomers
· Durable Industrial Elastomers: NDI prepolymers are widely used to produce high-performance elastomers that require extreme toughness, wear resistance, and the ability to withstand dynamic loads. These elastomers are used in industries such as automotive, aerospace, and industrial machinery.
2. Seals and Gaskets
· High-Temperature and Chemical-Resistant Seals: NDI-based polyurethanes are ideal for seals and gaskets that need to endure high temperatures, chemical exposure, and mechanical stress. These components are commonly used in engines, industrial pumps, and hydraulic systems.
3. Wheels and Rollers
· High-Wear Wheels: NDI prepolymers are often used in the manufacture of high-wear wheels and rollers for heavy-duty applications. Examples include forklift wheels, industrial conveyor rollers, and other load-bearing wheels subjected to constant wear and friction.
4. Conveyor Belts
· Durable and Abrasion-Resistant Belts: NDI-based polyurethane conveyor belts are known for their resistance to wear, abrasion, and chemical exposure, making them ideal for industries such as mining, food processing, and logistics where heavy-duty conveyors are needed.
5. Automotive Parts
· High-Temperature-Resistant Components: NDI prepolymers are used in the automotive industry to produce parts that require resistance to oils, fuels, and high operating temperatures. Examples include engine mounts, bushings, seals, and other components exposed to extreme conditions.
6. Aerospace Components
· High-Performance Polyurethanes for Aerospace: Due to their exceptional thermal stability and mechanical strength, NDI-based polyurethanes are used in aerospace applications where weight, durability, and performance under extreme conditions are critical.
7. Military and Defense Applications
· High-Durability Materials: NDI prepolymers are often used in military and defense applications for products such as armored vehicle components, tires, and high-performance elastomers. The materials’ ability to withstand extreme temperatures, mechanical stress, and chemical exposure makes them a preferred choice in this sector.
8. Footwear
· Durable Soles and Components: In high-performance and specialty footwear, NDI prepolymers are used to create durable soles, midsoles, and other components that require flexibility, abrasion resistance, and long-lasting performance, especially in high-endurance athletic or military footwear.
9. Medical Devices
· Biocompatible Elastomers: NDI-based polyurethanes are also used in certain medical devices due to their biocompatibility and durability. These materials can be found in products like medical tubing, catheters, and orthopedic devices where mechanical strength and resistance to body fluids are important.
Summary
NDI Prepolymers offer significant advantages in terms of mechanical strength, thermal stability, chemical resistance, and durability. These properties make them ideal for demanding applications in industries such as aerospace, automotive, military, and industrial manufacturing. Their ability to perform well in extreme environments and under continuous mechanical stress makes NDI prepolymers a preferred choice for high-performance polyurethane systems.