TDI-PPG and TDI-PTMEG Prepolymers
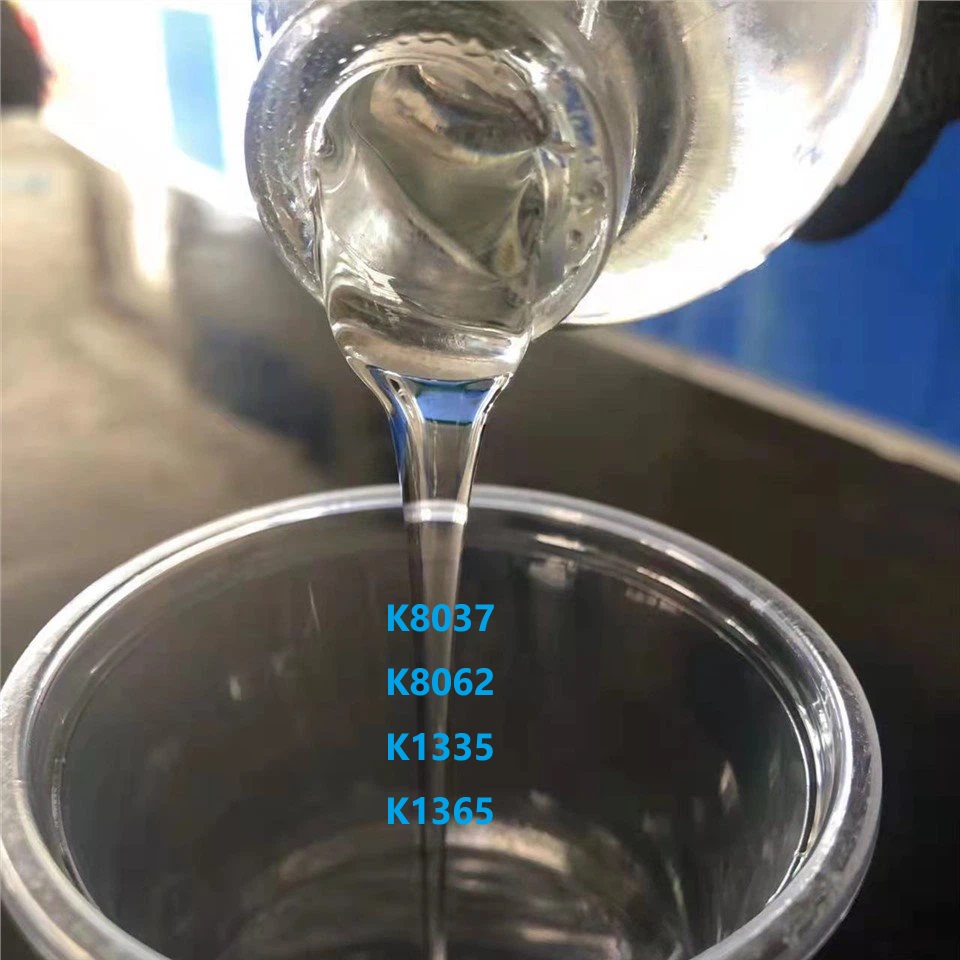
Index | K8037 | K8062 | K1335 | K1365 |
NCO Content (%) | 3.7±0.2 | 6.2±0.2 | 3.5±0.2 | 6.5±0.2 |
Operating Conditions | ||||
Ratio (Poly: BDO) | 100:10.59 | 100:17.74 | 100:10.02 | 100:18.60 |
Prepolymer Temp (°C) | 80 | 75 | 85 | 75 |
Curing Agent Temp (°C) | 115 | 115 | 115 | 115 |
Mold Temp (°C) | 100-110 | 100-110 | 100-110 | 100-110 |
Pot Life (min) | 8-12 | 2-4 | 13-18 | 3-5 |
After Cure (h/100°C) | 16-24 | 16-24 | 16-24 | 16-24 |
Physical Performance | ||||
Shore Hardness (A) | 80±2 | 95±2 | 85±2 | 97±2 |
100% Modulus (MPa) | 7-8 | 11-12 | 11-12 | 18-20 |
300% Modulus (MPa) | - | 20-21 | 18-20 | 40-43 |
Ultimate Elongation (%) | 260-300 | 350-420 | 360-420 | 250-300 |
Tensile Strength (MPa) | 12-15 | 22-26 | 25-28 | 10-46 |
Tear Strength (without Nick) (KN/m) | 50-55 | 85-95 | 60-65 | 95-105 |
Resilience (%) | 20-24 | 16-18 | 40-45 | 26-30 |
DIN Abrasion (mm³) | ≤160 | ≤130 | 40-45 | 36-40 |
Density (25℃) (g/cm³) | 1.10 | 1.10 | 1.11 | 1.12 |
TDI (Toluene Diisocyanate)-based prepolymers combined with PPG (Polypropylene Glycol) and PTMEG (Polytetramethylene Ether Glycol) offer distinct advantages due to the unique characteristics of each polyol type. Both types of prepolymers are commonly used in the production of polyurethane elastomers, foams, adhesives, and coatings. Here are the advantages and applications of TDI-PPG Prepolymers and TDI-PTMEG Prepolymers:
Advantages of TDI-PPG Prepolymers
1. Cost-Effective
· Economical Production: TDI-PPG prepolymers are often more cost-effective than other types of polyurethane prepolymers, making them suitable for large-scale production where cost control is important, such as in cushioning foams or lower-end elastomers.
2. Good Processability
· Ease of Processing: TDI-PPG systems are known for their easy processability, allowing for smooth and efficient manufacturing. These prepolymers cure rapidly, which can be an advantage in fast-paced production environments like the manufacture of flexible foams.
3. Good Flexibility
· Flexible Foams and Elastomers: TDI-PPG prepolymers are often used in the production of flexible foams and elastomers that offer good elasticity, making them suitable for applications requiring soft cushioning or flexible mechanical parts.
4. Moderate Chemical Resistance
· Resistance to Water and Some Chemicals: While PPG-based polyurethanes may not offer the same chemical resistance as PTMEG-based systems, they still perform reasonably well in environments with exposure to water and moderate chemicals, making them suitable for indoor applications or non-critical industrial uses.
5. Low Density
· Lightweight Components: TDI-PPG-based polyurethanes tend to produce lower-density foams and elastomers, which can be beneficial in applications requiring lightweight materials, such as cushioning and packaging.
Applications of TDI-PPG Prepolymers
1. Flexible Foams
· Cushioning Materials: TDI-PPG prepolymers are widely used in flexible polyurethane foams for furniture, mattresses, automotive seating, and packaging. These foams offer good elasticity and softness, making them ideal for comfort and cushioning applications.
2. Elastomers
· Moderate Performance Elastomers: TDI-PPG prepolymers are used to produce elastomers for general-purpose applications that do not require extreme chemical or temperature resistance, such as gaskets, seals, and bushings.
3. Adhesives and Coatings
· Adhesives with Good Flexibility: TDI-PPG prepolymers are used in adhesives that require flexibility and moderate chemical resistance. These adhesives can be used in non-critical bonding applications, such as in packaging or furniture assembly.
4. Packaging Foams
· Protective Packaging: The low density and flexibility of TDI-PPG foams make them suitable for protective packaging solutions, especially in the electronics, consumer goods, and automotive industries.
Advantages of TDI-PTMEG Prepolymers
1. Superior Mechanical Properties
· High Tensile Strength and Toughness: TDI-PTMEG prepolymers provide polyurethane systems with superior tensile strength and toughness compared to TDI-PPG systems. This makes them suitable for high-performance applications that require durability and the ability to withstand heavy mechanical stress.
2. Excellent Hydrolysis Resistance
· Superior Water Resistance: PTMEG-based polyurethanes have outstanding hydrolysis resistance, meaning they are stable and maintain their mechanical properties even in moist or wet environments. This makes them ideal for outdoor or underwater applications where moisture exposure is a concern.
3. Exceptional Low-Temperature Flexibility
· Performance in Cold Environments: TDI-PTMEG prepolymers maintain flexibility and elasticity at low temperatures, making them suitable for applications in cold climates or refrigeration environments. They do not become brittle at low temperatures, unlike some other polyurethane systems.
4. High Abrasion and Tear Resistance
· Durability in High-Wear Applications: TDI-PTMEG prepolymers exhibit superior resistance to abrasion and tearing, making them ideal for applications where components are subjected to constant wear and mechanical stress, such as industrial rollers and seals.
5. Good Chemical Resistance
· Resistant to Oils and Fuels: PTMEG-based polyurethanes are highly resistant to oils, fuels, and many chemicals. This characteristic is essential for automotive, industrial, and marine applications where exposure to aggressive substances is common.
6. Long-Term Elasticity
· Excellent Dynamic Properties: TDI-PTMEG prepolymers provide long-term elasticity and dynamic performance. This means the material can endure repeated deformations, vibrations, and dynamic loading without losing its shape or mechanical properties, making it suitable for high-performance elastomers.
Applications of TDI-PTMEG Prepolymers
1. High-Performance Elastomers
· Durable Elastomers for Harsh Conditions: TDI-PTMEG prepolymers are used to create elastomers for demanding applications requiring superior mechanical properties, such as industrial rollers, gaskets, seals, and bushings. These elastomers are often found in automotive, aerospace, and heavy machinery applications.
2. Seals and Gaskets
· Chemical-Resistant Seals: Due to their high chemical and hydrolysis resistance, TDI-PTMEG-based polyurethanes are used in seals and gaskets that need to withstand harsh chemical environments, high temperatures, and exposure to water or oils. These parts are used in industries such as oil and gas, automotive, and marine.
3. Wheels and Tires
· Wear-Resistant Wheels: TDI-PTMEG prepolymers are used to produce wheels and tires for heavy-duty applications that demand high abrasion resistance and durability, such as industrial carts, forklifts, and even recreational products like skateboards.
4. Hoses and Tubing
· Flexible, Chemical-Resistant Tubing: TDI-PTMEG-based polyurethanes are used in the manufacture of flexible hoses and tubing that require resistance to chemicals, oils, and fuels. These components are widely used in fuel systems, hydraulic systems, and industrial chemical transport.
5. Coatings
· Protective Coatings: TDI-PTMEG prepolymers are also used in creating protective polyurethane coatings that provide abrasion resistance, chemical protection, and flexibility. These coatings are applied to industrial equipment, pipelines, and other surfaces that require long-term protection from wear and corrosion.
6. Adhesives
· High-Performance Adhesives: TDI-PTMEG prepolymers are used in adhesives that require superior bonding strength and flexibility under dynamic loads, as well as resistance to oils and chemicals. These adhesives are common in the automotive and aerospace industries.
Summary
TDI-PPG Prepolymers offer a cost-effective solution for general-purpose polyurethane applications, particularly in flexible foams and elastomers where mechanical demands are moderate. Their ease of processing and good flexibility make them ideal for cushioning and packaging applications.
On the other hand, TDI-PTMEG Prepolymers provide superior mechanical properties, exceptional hydrolysis resistance, and excellent performance in harsh environments. They are preferred for high-performance elastomers, seals, gaskets, and other applications requiring durability, abrasion resistance, and chemical stability, particularly in demanding industries such as automotive, aerospace, and industrial manufacturing.